Understanding EDI 940: Warehouse Shipping Order
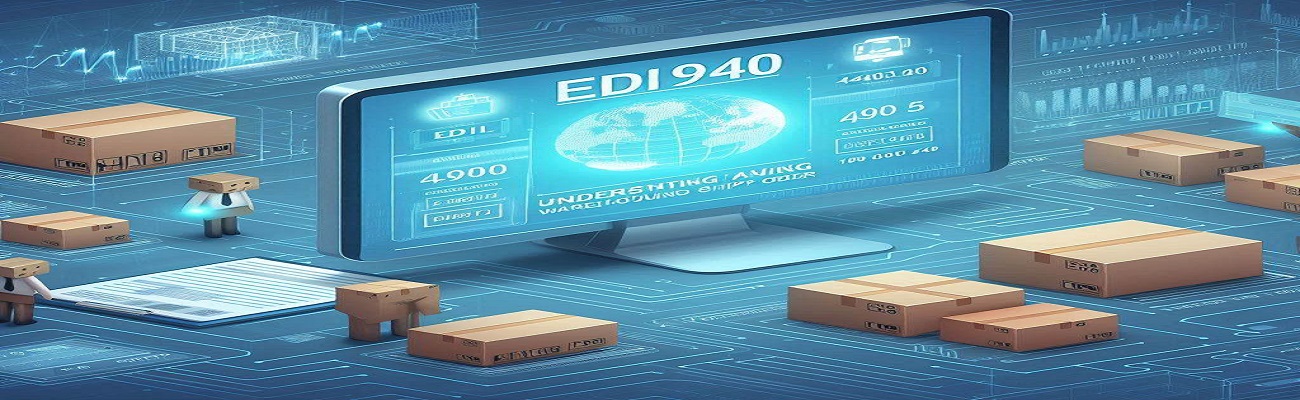
Updated On 22 Mar, 2025
Introduction
In the realm of supply chain management and Electronic Data Interchange (EDI), automation and timely communication are essential for efficient operations. One important transaction set that plays a vital role in warehouse management is EDI 940, or Warehouse Shipping Order. This transaction allows trading partners to communicate detailed shipping instructions to a third-party warehouse, ensuring that orders are processed and shipped accurately.
In this blog, we’ll take a deep dive into what EDI 940 is, its purpose, structure, and the significant benefits it offers for streamlining warehouse shipping operations.
What is EDI 940?
EDI 940, or the Warehouse Shipping Order, is an electronic document used by a company to instruct a third-party warehouse or logistics provider to ship goods to a specific destination. It outlines important shipping details such as:
- Items to be shipped
- Quantities
- Shipping method
Example Scenario
When a retailer receives a customer order, they may send an EDI 940 to their third-party logistics (3PL) provider or warehouse partner to pick, pack, and ship the goods on their behalf.
Purpose of EDI 940
The primary purpose of EDI 940 is to automate the communication of shipping instructions between businesses and warehouses. It eliminates manual paperwork, reducing errors and ensuring faster processing.
Key Goals of EDI 940:
- Providing Detailed Shipping Instructions – Specifies items, quantities, and delivery details.
- Facilitating Timely Order Fulfillment – Ensures accurate and prompt order processing.
- Supporting Multiple Shipping Scenarios – Manages partial shipments, special instructions, and multiple locations.
- Improving Inventory Management – Synchronizes stock levels between the company and warehouse.
Key Components of EDI 940
Like other EDI transactions, EDI 940 follows a structured format composed of various segments, each carrying essential shipping details.
Main Components of an EDI 940 Transaction:
- ST (Transaction Set Header) – Identifies the document as an EDI 940.
- W05 (Shipping Order Identification) – Includes order number, date, and shipping method.
- N1 (Party Identification) – Identifies the shipper, consignee, and third-party warehouse.
- LX (Transaction Set Line Number) – Details about the line items in the order.
- W06 (Line Item Detail) – Specifies item numbers, descriptions, quantities, and packaging details.
- TD5 (Carrier Information) – Provides shipping method and carrier details.
- N9 (Reference Identification) – Includes reference numbers and special handling instructions.
- SE (Transaction Set Trailer) – Marks the end of the EDI 940 document.
EDI 940 Workflow Example
To better understand how EDI 940 fits into warehouse and logistics operations, let’s walk through a typical workflow scenario:
- Order Received – A retailer receives a customer order.
- Create EDI 940 – The retailer generates an EDI 940 document containing shipping details.
- Send EDI 940 to Warehouse – The retailer transmits the document to a third-party warehouse.
- Warehouse Processes the Order – The warehouse picks, packs, and prepares the shipment.
- Warehouse Sends EDI 945 – Once shipped, the warehouse sends back EDI 945 (Warehouse Shipping Advice) confirming fulfillment.
Benefits of EDI 940
- Faster Order Fulfillment – Automates the process, ensuring shipments reach customers quickly.
- Reduced Manual Errors – Eliminates manual data entry, reducing errors in shipping details.
- Enhanced Communication – Real-time updates between businesses and warehouses for faster processing.
- Improved Inventory Management – Keeps stock levels updated, preventing overselling or stock shortages.
- Cost Efficiency – Reduces labor costs and increases operational efficiency.
- Greater Flexibility – Supports split shipments, partial orders, and special shipping instructions.
EDI 940 vs. EDI 945
While EDI 940 provides shipping instructions, it is closely related to EDI 945 (Warehouse Shipping Advice).
EDI 940 | EDI 945 |
---|---|
Sent to the warehouse to instruct shipping | Sent from the warehouse to confirm shipment |
Contains order details, shipping instructions | Confirms items shipped, tracking info |
Initiates the fulfillment process | Completes the fulfillment process |
Conclusion
EDI 940 plays a critical role in automating warehouse shipping operations by ensuring that businesses can quickly and accurately transmit shipping instructions to their logistics providers.
By implementing EDI 940, businesses can:
- ✅ Improve order fulfillment times
- ✅ Reduce manual errors
- ✅ Enhance inventory management
- ✅ Streamline communication with warehouse partners
In today’s fast-paced supply chain environment, EDI 940 is an essential tool for businesses that want to stay ahead of the competition.