Common EDI 850 Purchase Order Errors and How to Avoid Them
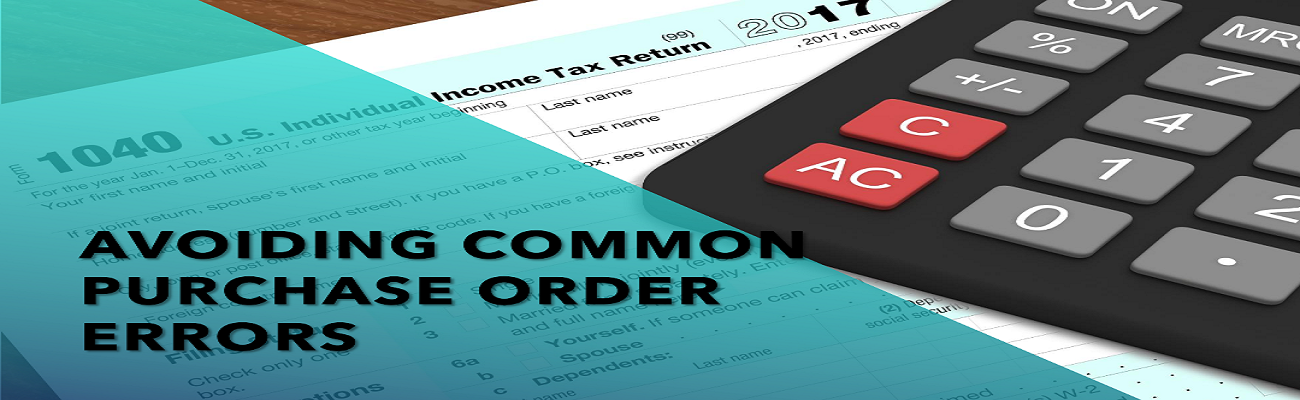
Updated On 21 Mar, 2025
Introduction
Electronic Data Interchange (EDI) has become the backbone of modern supply chain communication, especially when it comes to transmitting purchase orders between trading partners. The EDI 850 Purchase Order allows companies to automate and streamline their procurement process, improving efficiency and reducing manual errors. However, like any technology-driven process, EDI 850 transactions can sometimes encounter issues. Understanding common EDI 850 errors and how to avoid them is crucial to ensuring smooth operations.
In this blog, we’ll explore some of the most frequent EDI 850 errors, why they happen, and how you can avoid these common EDI mistakes to keep your supply chain running smoothly.
Common EDI 850 Purchase Order Errors
1. Missing or Incorrect Data
Problem: One of the most common EDI 850 errors is missing or incorrect data in the transaction. This could include incomplete addresses, missing line item details, or incorrect product codes. Missing critical data can result in delayed shipments, incorrect orders, or processing failures.
How to Avoid: Implement strict validation checks before sending an EDI 850 transaction. Use automated software that flags missing fields or incorrect data, and ensure all data elements comply with your trading partner’s EDI standards.
2. Incorrect Segment Formatting
Problem: EDI 850 transactions have specific formatting rules for each data segment. If the data is not properly formatted—such as using the wrong date format or incorrectly structured item quantities—the receiving system may reject the entire transaction.
How to Avoid: Ensure your EDI software is configured to automatically format data according to the required standards. Most EDI systems include built-in validation for formatting errors, which can help prevent incorrect segment structuring.
3. Duplicate Purchase Orders
Problem: Sending duplicate EDI 850 purchase orders can create confusion and lead to unnecessary shipments or production runs. This usually occurs when there is a system glitch or miscommunication between departments.
How to Avoid: Implement a system that checks for duplicate purchase orders before submission. Setting up unique purchase order identifiers can help track orders and avoid sending multiple copies of the same transaction.
4. Mismatched Product Codes
Problem: When the product codes in the EDI 850 do not match the supplier's catalog, the transaction can fail or result in incorrect items being shipped. This can be due to outdated product catalogs or human error during data entry.
How to Avoid: Maintain an updated product code database, and ensure that your EDI 850 transactions pull product data from the latest catalog. Regular synchronization between buyers and suppliers can prevent these mismatches.
5. Invalid or Expired Purchase Order Numbers
Problem: If the purchase order number used in the EDI 850 has already been used or is no longer valid, the transaction may be rejected by the trading partner’s system.
How to Avoid: Implement a system that tracks purchase order numbers to ensure they are valid and unique. Automated validation checks before sending the EDI 850 can prevent the use of invalid or expired numbers.
6. Incorrect Pricing or Quantity
Problem: Another common EDI 850 error is sending incorrect pricing or quantity information. This could lead to financial disputes, overproduction, or under-shipment.
How to Avoid: Ensure that your pricing and quantity data is accurate by integrating your EDI system with your inventory management and pricing systems. Automated checks and balances can help prevent these types of discrepancies.
7. EDI Acknowledgment Failures
Problem: After sending an EDI 850, the supplier is expected to respond with an EDI 997 Functional Acknowledgment or an EDI 855 Purchase Order Acknowledgment. If these acknowledgments are not received, it can indicate an issue with the original transaction.
How to Avoid: Set up a monitoring system that automatically tracks acknowledgments for every EDI 850 transaction. If no acknowledgment is received within a specified time frame, trigger an alert to investigate the issue.
EDI 850 Troubleshooting: How to Fix Common Errors
1. Use EDI Software with Built-in Error Detection
Most modern EDI solutions come equipped with error detection features that automatically scan for potential issues before transmitting data. This is a vital tool for catching errors related to missing fields, incorrect formatting, or invalid product codes. Investing in robust EDI software that offers these capabilities will save you from costly mistakes down the line.
2. Set Up Validation Rules
Configure your EDI system to validate all data before transmission. This could include checking for missing data fields, duplicate purchase orders, and ensuring product codes match the latest catalog. Establish validation rules that align with your trading partners' requirements to ensure smoother transactions.
3. Monitor Acknowledgments and Status Codes
Tracking acknowledgments such as the EDI 997 Functional Acknowledgment and EDI 855 Purchase Order Acknowledgment is crucial for catching potential issues. Regular monitoring of these status updates can help identify problems early, allowing you to resolve them before they escalate.
4. Perform Regular Data Audits
Data audits can help prevent many EDI 850 errors, especially those related to outdated product codes, pricing, or shipping information. Set a regular schedule to audit your data for accuracy and make necessary updates.
5. Establish Strong Communication with Trading Partners
A significant portion of EDI errors can be avoided by establishing clear communication lines with your trading partners. Regularly sync up on data formats, updates to catalogs, and any changes in your partner’s EDI requirements to prevent potential mismatches or miscommunication.
How to Avoid Common EDI Mistakes
- Standardize Processes: Ensure that your EDI processes are standardized across your organization. Standardization helps reduce human errors and ensures consistency.
- Automate Where Possible: Automation significantly reduces the risk of manual errors in EDI transactions. By automating processes like validation, formatting, and data entry, you can minimize common EDI mistakes.
- Regular Training: Keep your team informed about EDI best practices and errors to watch out for. Continuous training ensures that employees stay updated on new processes and technologies.
Conclusion
While EDI 850 offers significant benefits in streamlining purchase order transactions, errors can occasionally occur, disrupting the supply chain. By understanding the common EDI 850 errors and implementing best practices, businesses can significantly reduce these issues and maintain efficient, error-free EDI transactions.
Avoiding common EDI mistakes requires the right combination of robust EDI software, regular data validation, b communication with trading partners, and automation to streamline processes. With these steps in place, your business will be well-equipped to handle EDI 850 purchase orders smoothly.
Need Help with EDI 850?
If you’re experiencing issues with your EDI 850 purchase orders or need guidance on how to set up a robust EDI system, our EDI experts are here to help. Contact us for a consultation to optimize your EDI processes and ensure error-free transactions.